Impact of material change on thermo-structural behaviour of F-class gas turbine discs,
Bachelor's Thesis.
Jul 25, 2024 ・ 2 min read
Overview
This research, conducted in collaboration with EthosEnergy S.p.A., aims to perform a thermo-structural analiysis focusing on the behavior of turbine discs in response to changes in their constituent materials. The specific
components under analysis are the discs of a FR1500 gas turbine Figure 1, manufactured by EthosEnergy S.p.A.
at their facility in Settimo Torinese (TO).
The FR1500 gas turbines commenced their commercial operation in
1990 and continue to be operational and producing electricity nowadays. With over 950 installed units, these
turbines collectively generate approximately 175 GW of power across 11 countries. The purpose of the thesis is
to assess the advantages and disadvantages of transitioning from the NiCrFe alloy - NiCrFe alloy to the NiCoCr
alloy - NiCoCr alloy for the production of turbine components.
The primary objective is to evaluate the thermal and structural impacts on the rotor throughout its operational cycle, from start-up to shutdown, utilizing 2D thermal-structural analyses with ANSYS
Mechanical .
Emphasis will be placed on examining stresses and deformations for both possible materials, comparing them against design tolerances and material limit curves to assess their acceptability. The comparative
analysis of the resulting data will help determine whether one of the examined materials is more suitable than
the other for the specific application or if both materials are equally viable.
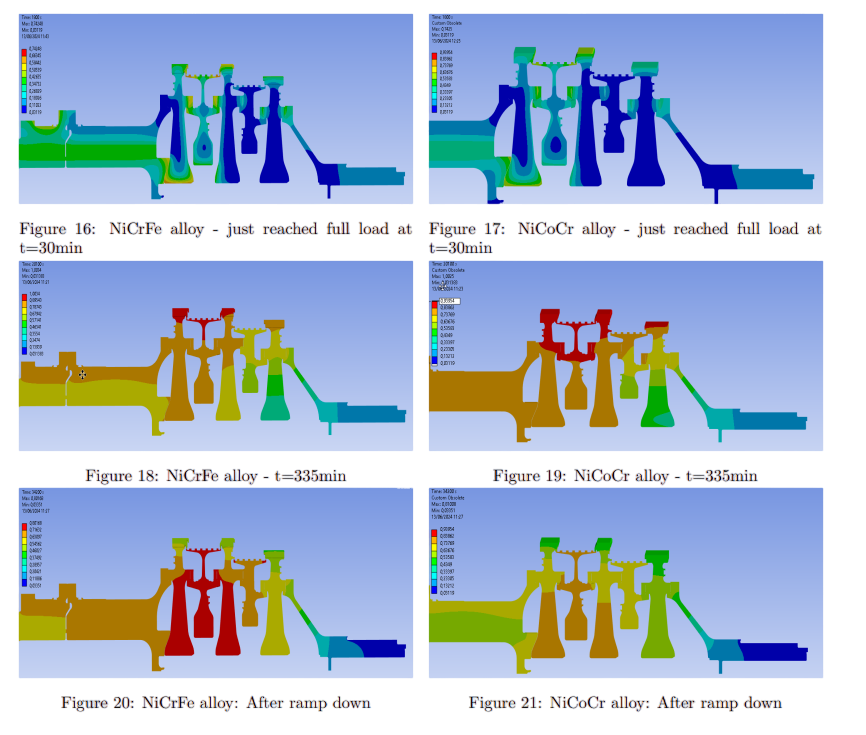
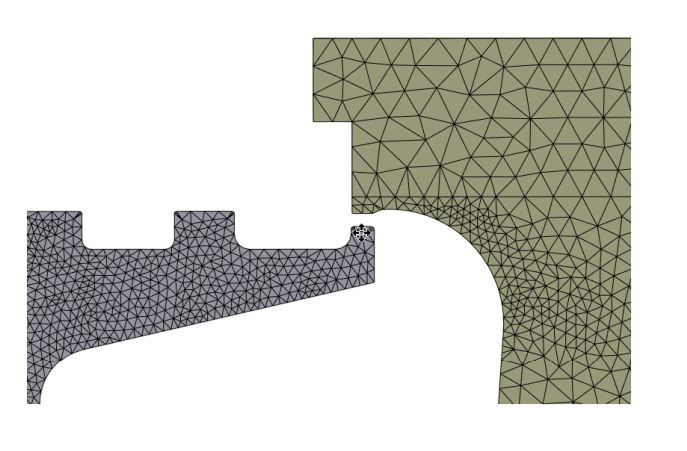
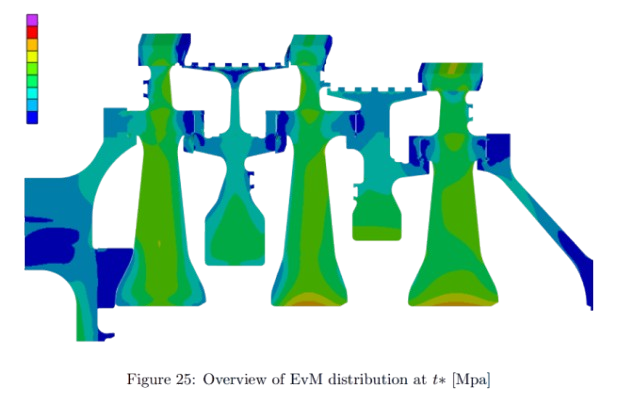
Simulations
The simulation is performed as a 2D transient analysis and then rotated 360° to assume axisymmetry, reducing computational complexity compared to 3D.
However, some geometries, like turbine disk cavities, do not satisfy axisymmetry, requiring a plane stress condition.
Through-holes for tie rods are modeled using orthotropic stiffness, adjusting Young’s modulus based on an area ratio calculation.
This ensures accurate representation of reduced stiffness and stress concentrations.
If the disk were revolved, it would appear solid, making it crucial to assign degraded material properties to perforated sections for realistic simulations.
Key Results
- ✔️ demonstrated higher fatigue resistance in high-temperature conditions.
- ✔️ NiCoCr exhibited easier machining properties but higher deformation risks.
- ✔️ 3D steady-state simulations recommended for critical components.
- ✔️ NiCrFe remains the preferred material for high-temperature applications.